저전력, 저비용, 단시간을 한꺼번에 이루는 스마트한 공장
글로벌 네트워크기업 시스코에서 예상한 사물 인터넷(IoT)의 잠재가치는 자그마치 14조 달러이다. 그 중 스마트 공장 부분이 27%인 3조 8000억달러를 차지하고 있다. 스마트공장은 초연결, 융합을 통해 구현되는데, 가장 기반이 되는 기술이 바로 IoT이다.
사물인터넷은 모든 산업들을 변화시키고 있다. 눈깜짝할 사이에 생활 깊숙이 자리 잡고 우리의 삶을 제어하고 통제가 가능해질 것이다. 이러한 사회 변화들이 급격하게 일어날 때는 터닝포인트가 있기 마련이다.
스마트공장도 제조업의 터닝포인트가 될 것이다. 스마트 제조기술을 구현하느냐 마느냐의 문제는 향 후 기업 존속이 달려있기 때문이다. 무엇보다 이 사업의 핵심은 초연결과 초융합이다. 가장 쉬운 예로 스마트폰이 친구, 회사 가족 등과 다 연결되고 앱을 통해서 모든 것을 다할 수 있게 되었다. 심지어 고화질 카메라에 녹음은 기본이고 신용결제도 가능하게 된 것처럼 말이다. 이를 공장에도 적용된다면, 앞으로 기계들의 자율적인 지능형 공장시대가 열릴 것이다.
제조업의 터닝포인트 ‘초연결, 초융합’
IoT 시장의 스마트공장, 제조, 생산과 관련된 부분이 27%로 가장 크다. 금액으로 환산하면 3조8000억 달러에 해당되고 이 금액은 앞으로 자산활용, 고용, 생산성, 공급망 물류, 고객, 가치혁신등 제조와 생산에 관련된 포괄적인 부분에 투자될 것이다. 하지만 제조업의 인프라 구축은 무엇보다도 꾸준하고 구체적일 필요가 있다. 현재 어떻게 진행되고 있는지 11월 5일에 열린 스마트제조기술전에서 정부의 스마트공장 보급 확산 정책 세미나를 통해 우리나라의 투자 그리고 현황에 대해 알 수 있었다. 발표는 산업통상자원부 이규봉 팀장이 맡았다.
먼저 스마트공장의 개념은 IoT,CPS(가상물리시스템)기반 자동화 + 디지털화”를 지향한다. 스마트공장을 기획, 설계, 생산, 유통, 판매 등 전 과정을 ICT로 통합할 수 있다.
2020년까지 1만개 공장으로 확대
이에 맞춰 정부는 스마트공장 보급 및 확산을 위해 경제단체, 수요대기업, 중소기업 등으로 ‘스마트공장 추진단’을 구성하였다. 민관 공동 1조원 규모이며 산업혁신운동 3.0 추진체계를 활용, 중소, 중견기업 보급을 추진하고 있다.
스마트공장 보급 확산은 2020년까지 1만개 공장을 스마트화 할 계획이다. 시제품과 생산품에도 기여할 3D프린팅 생산기반 확충을 통해 6개 거점별 제조혁신센터를 구축하여 산업 재직자나 예비 창업자 대상 3D프린팅 인력양성을 추진 한다. 또한 핵심 기반이 되는 SW, 센서, 솔루션 등의 고부가가치 산업화 노력도 병행된다.
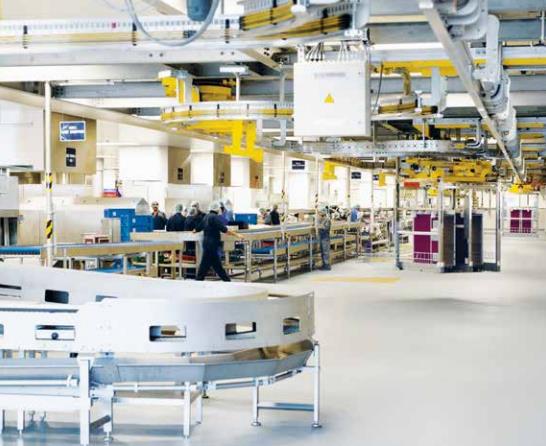
▶ 지멘스 스마트 팩토리
현재 유럽 최고 스마트공장으로 인정받고 있는 지맨스 암벡(Amberg)공장에서는 자동화율 75%를 달성하여 제품과 생산설비의 실시간 교신체계가 되어있다. 다품종 대량생산이 가능하여 1,000여개 종료 제품을 연간 1,200만개 생산하는 동시에 약 30% 에너지를 줄인다.
그러나 “시스템의 자동화는 대부분 고가용 장비들이기 때문에 프로젝트를 통하여 자동화 기계를 구매할 때 융자를 받을 수 있다”고 말했다. 그리고 정부에서는 120개 회사의 툴을 가지고 있기 때문에 툴 내에서 기업 프로젝트를 공정히 선정 한다”고 밝혔다.
기업들이 추진하는 프로젝트에는 작년 반월공단 사례에서 기존의 주조공장 장비에 데이터게더링 디바이스와 시스템을 구축하여 작업 데이터관리를 정보화 할 수 있었다.이렇게 정보화된 데이터들은 클라우드 사업을 통해 보급 모델 프로젝트를 강화시킨다. 이미 시작 된 상태이며 통신사와 함께 수집된 정보를 통해서 피드백이 가능한 빅데이터로 이용 할 수 있도록 하는 것이다.
생산시간 60분 → 5분 92%감소
박규봉 팀장은 2014 보급사업 성과를 보고하면서 “자동차부품 제조 I사는 33%정도 품질개선이 되었다. 생산운영 관리 시스템(MES, ERP, POP, SPC)구축으로 불량률이 50%나 감소했고 열처리 업체 S사는 비용을 23% 절감했다”고 말했다. 이유는 전력감시 모니터링 시스템 도입 후 공정 효율화, 자동화로 에너지를 사용하고 재고량과 물류비 등 원가 비용 등을 포함하여 30% (연간 8천만원)을 줄일 수 있었기 때문이다. 납기 또한 20% 단축하였는데 “전자부품 제조 G사는 설계자동화시스템(PLM) 도입 후 수기로 작성하던 작업지시서를 자동화시키면서 1개 모델 생산시간이 60분이었던 것을 5분으로 단축하여 92%의 놀라운 단축 효과를 보여주었다.”고 그는 말했다.
마지막으로 그는 위의 그림처럼 향후 스마트공장은 보급 정책은 크게 두 가지로 나뉘는데 “예를 들어 100개를 만든다면, 20개 정도는 고도화된 스마트 공장을 세우면서 R&D 방향으로 나가고 나머지 80개는 실질적으로 수요가능한 보편적인 모델을 보급해 나갈 방침이다”라고 전했다.