높은 배터리 비용에도 불구하고 전체 자동차 판매량 중 배터리 구동 차량의 비중은 현재 1% 미만에서 2025년에 최대 10%까지 높아질 전망이다. 전기자동차 전체 제조비용에서 배터리 비용은 거의 절반을 차지한다. 배터리 비용의 최대 20%를 차지하는 배터리 활성화와 테스트 단계를 개선할 수 있다면, 배터리 비용을 크게 줄일 수 있을 것이다. 전기자동차 배터리 제조사들은 배터리 활성화 및 테스트 시스템 전문지식을 갖춘 공급사와의 협력을 통해 그 비용을 줄일 수 있다.
배터리, 전기자동차 전체 제조비용의 절반 차지
제조비용 줄이려면 통합적인 접근 방법 취해야
AD8452, 시스템 풋 프린트 50% 절감 가능해
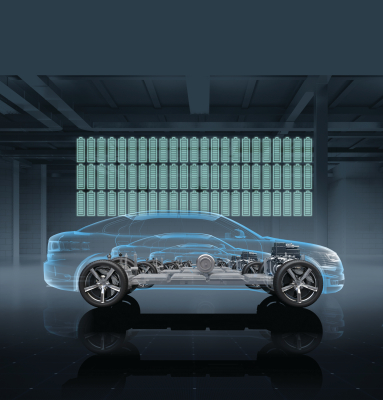
배터리 비용은 전기자동차 생산비용 중 거의 절반을 차지한다
이산화탄소 배출 규정이 갈수록 엄격해지고 환경에 대한 소비자들의 의식이 높아지면서 전기자동차로의 전환이 빨라지고 있다.
전체 자동차 판매량 중 배터리 구동 차량의 비중은 현재 1% 미만에서 2025년에는 최대 10%까지 높아질 전망이다. 높은 배터리 비용에도 불구하고 말이다. 전기자동차 전체 제조비용에서 배터리 비용은 거의 절반을 차지한다.
배터리 가격을 결정하는 요인들은 많다. 하지만 제조사들이 비용을 줄이는 데 가장 많은 진전을 이룰 수 있는 부분이 바로 마지막 생산 단계다. 특히 배터리 활성화와 테스트 단계는 전기자동차 배터리 비용의 최대 20%를 차지한다.
배터리 활성화와 테스트는 많은 시간이 소요되는 공정으로 배터리 화합물을 활성화하는 여러 번의 충전과 방전을 포함하며 최대 이틀이 걸릴 수 있다. 이 필수적인 절차는 배터리를 사용하기 위해 준비하고, 배터리의 신뢰성과 품질을 보장하는 데 있어서 매우 중요하다.
이 작업은 그러나 느린 공정 진행 속도 때문에, 배터리 제조사가 전반적인 제조비용을 낮출 수 있을 정도로 높은 생산력을 달성하지 못하게 하는 심각한 병목 지점이 된다.
따라서 전기자동차 배터리 제조사들은 배터리 활성화 및 테스트 시스템 전문지식을 갖춘 공급사와의 협력을 통해 핵심적인 생산 단계와 관련된 시간과 비용을 절감하면서 첨단 배터리 화합물에 요구되는 정밀성을 유지할 수 있다.
배터리 비용을 낮추는 높은 처리율
배터리 비용을 낮추기 위해 제조사는 통합적인 접근 방법을 취할 필요가 있다. 이를 통해 공급사의 시스템 레벨 전문성을 활용하여 전체 배터리 테스트 회로의 풋 프린트를 줄이면서 채널 숫자를 늘릴 수 있다. 이들 모두 배터리 활성화의 정확도, 정밀도, 신뢰성 및 속도를 유지하면서 안전, 성능 및 신뢰성 요건을 충족하도록 시험 측정을 수행해야 한다.
물론 쉽지 않다. 프런트엔드에서 배터리 충전 회로를 구동하는 전원은 엄격하게 제어되어야 한다. 더 깊이 들어가면, 배터리 활성화와 테스트는 배터리의 과 충전과 미달충전을 방지하기 위해 배터리 사이클 동안 사용되는 전류 및 전압 프로파일을 정밀하게 모니터링 해야 한다. 이렇게 하면 테스트 작업 동안 안전을 보장하고, 배터리 수명을 극대화할 수 있어 최종 사용자의 전체 소유 비용을 크게 낮출 수 있다.
중요한 배터리 측정의 경우 혹독한 공장 환경에서도 ±0.05% 이상의 정확도로 배터리 충전 및 방전 전류를 측정할 수 있도록 매우 높은 품질의 계측 증폭기(in-amp) 및 관련된 션트 저항이 필요하다. 동일한 수준의 정확도가 전체 열 동작 범위에서 전압을 모니터링 하는 데 사용되는 차동 증폭기에 적용된다.
이러한 부품을 하나의 솔루션으로 통합하는 방법에는 여러 가지가 있지만, 성능을 극대화하면서 시스템 풋 프린트를 최소화하는 것은 상당히 어렵다. ADI가 아날로그 프런트엔드, 전원 제어 및 모니터링 회로를 단일 IC AD8452에 통합한 이유다.
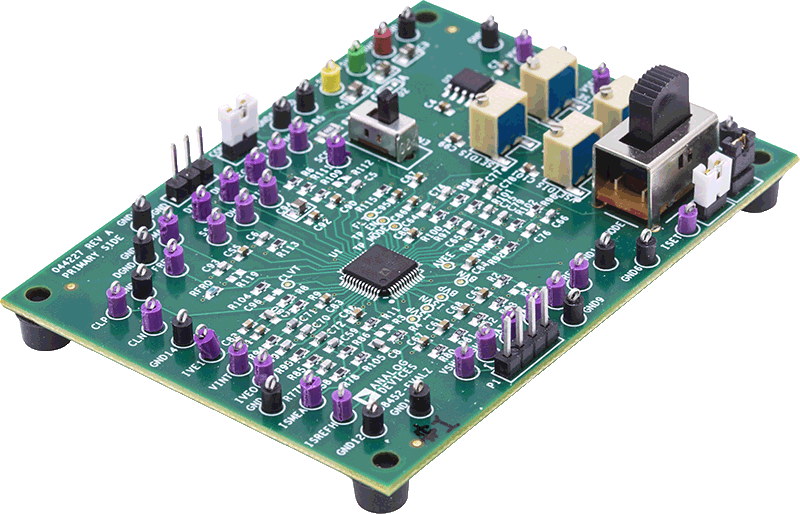
ADI AD8452 평가보드
AD8452는 배터리 역극성 방지, 과전압 보호 스위치, 그리고 배터리 과 충전을 방지하기 위한 스마트 제어를 포함하고 있으며 시스템 풋 프린트를 50% 절감할 수 있다. 이러한 통합된 기능을 이용하면 배터리 제조사는 더 많은 기능을 테스트 시스템에 통합함과 동시에, 공장 작업장 공간을 더 효율적으로 사용할 수 있게 된다. 뿐만 아니라 이를 통해 제조사는 더 많은 기능과 더 견고한 테스트 절차를 갖춘 시스템을 설계할 수 있다.
효율적인 전력 변환은 시스템 성능을 높일 수 있는 또 다른 기회다. 향상된 스위칭 아키텍처를 통해 테스트 시스템은 그리드와 양방향으로 에너지를 교환할 수 있게 돼 전력 소모를 최소화할 수 있다.
또 효율적인 전력 변환은 시스템의 전체 비용과 전력 소모에 추가되는 열 관리 장치의 필요를 줄인다. 낭비되는 에너지와 생산 비용이 감소하는 것이다. 이러한 기능을 구현하기 위해서는 새로운 탄화규소(SiC)나 질화갈륨(GaN) 전원 스위칭 기술의 빠른 스위칭 요구를 지원하는 절연 게이트 드라이버와 같은 시스템 특성에 대한 이해가 필요하다.
시스템 레벨의 전문지식과 광범위한 제품 포트폴리오를 갖춘 공급사와 긴밀히 협력하는 것은 단순히 더 정교한 부품과 빌딩 블록을 활용할 수 있는 것 이상의 이점을 제공한다. 이 경우, 배터리 제조사는 보다 쉽게 채택할 수 있는 시스템 아키텍처를 위한 레퍼런스 디자인을 이용할 수 있는데, 배터리 활성화 및 테스트 시스템을 처음부터 스스로 개발해야 하는 경우보다 3~4배 더 빨리 제품을 출시할 수 있다.
전 세계의 전기자동차 수요가 2021년까지 연평균 21%씩 성장할 것으로 보임에 따라 배터리 제조사와 공급사 간의 긴밀한 협력의 필요성이 그 어느 때보다 높아지고 있다.
공급사는 제조사의 시스템이 새로운 수준의 효율을 달성할 수 있도록 신뢰성 높은 검증된 솔루션을 제공할 필요가 있다. 최고의 공급사는 제조사가 이러한 새로운 기능을 보다 빨리 출시하도록 도울 수 있으며, 이를 통해 배터리와 전기자동차 생산이 모두 증대되는 성과를 이루는 데 기여할 수 있다.
이 기사는 아나로그디바이스의 엔지니어, 비카스 초우드리(Vikas Choudhary)의 글 ‘전기자동차 생산 확대에 필수적인 첨단 배터리 활성화 및 테스트 시스템(Scaling Electric Vehicle Production Requires Advanced Battery Formation and Test Systems)’을 정리한 것입니다.