IO-Link, 아날로그 센서 지능형 센서 탈바꿈
최신 트랜시버, 고효율 DC-DC 벅 레귤레이터 통합·발열 특성 개선
IO-Link 기술, 디바이스 규격 작고·견고하며·전력 효율적 센서 중요
■ IO-Link, 산업용 센서를 위한 새로운 표준으로서 빠른 성장
전통적으로 산업용 센서는 아날로그였으며, 지금도 많은 경우 아날로그이다.
산업용 센서는 기본적으로 센싱 장치와 센싱 데이터를 컨트롤러로 전달하기 위한 장치들로 이루어진다.
데이터는 단방향 아날로그였다. 그 후 바이너리 센서가 등장했다. 바이너리 센서는 디지털 온/오프 신호를 제공하며 유도식, 정전용량식, 초음파, 광전 방식 등의 센싱 장치와 반도체 스위칭 소자를 포함했다. 출력은 상측(HS) 스위칭(PNP)이나 하측(LS) 스위칭(NPN), 또는 푸시-풀(PP)이었다.
하지만 데이터는 여전히 센서에서 마스터로 단방향 통신으로 제한되었고, 오류 제어가 불가능했으며, 수동 캘리브레이션 같은 작업을 위해 현장에 기사가 파견되어야 했다.
최근에는 ‘인더스트리 4.0’, 스마트 센서, 재설정 가능한 공장 설비 같은 요구 사항을 충족하기 위해서 진보된 솔루션이 필요해졌다.
이러한 솔루션을 제시하는 것이 바로 IO-Link 프로토콜이다. IO-Link는 산업용 센서를 위한 비교적 새로운 표준으로서 빠른 성장 속도를 나타내고 있다.
IO-Link 컨소시엄은 지금까지 1,600만 개 이상의 IO-Link 지원 노드가 현장에서 사용되고 있는 것으로 추산하고 있으며, 그 수는 계속해서 늘고 있다.
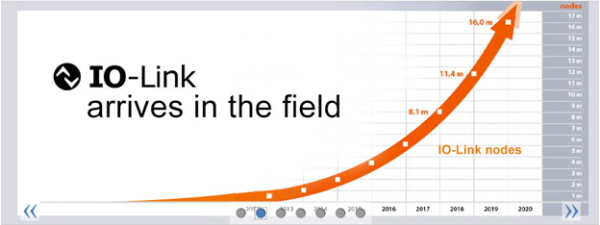
▲그림 1 : IO-Link 프로토콜의 급격한 성장세(출처 : IO-Link 컨소시엄, https://io-link.com/en/)
IO-Link는 IEC 61131-9로 표준화되었으며, 산업용 시스템에서 센서와 액추에이터가 컨트롤러와 어떻게 상호작용할지 정의하고 있다.
IO-Link는 표준화된 커넥터, 케이블, 프로토콜을 사용한 점대점(point-to-point) 통신 링크이다. IO-Link 시스템은 산업 표준 3-와이어 센서 및 액추에이터 인프라 내에서 작동하도록 설계되었으며, IO-Link 마스터와 IO-Link 디바이스 제품으로 구성된다.
IO-Link 통신은 한 개의 마스터와 한 개의 디바이스(센서나 액추에이터) 사이에서 이루어진다.
통신은 바이너리(반이중)이며 비차폐 케이블을 사용해서 20미터 이내의 거리로 제한된다.
통신을 위해서는 3-와이어 인터페이스(L+, C/Q, L-)가 필요하다. IO-Link 시스템에서 전원 범위는 마스터는 20∼30V이고, 디바이스(센서나 액추에이터)는 18∼30V이다.
아나로그디바이스(Analog Devices)의 IO-Link 핸드북1에서는 IO-Link의 장점에 대해서 다음과 같이 설명하고 있다.
“IO-Link는 기존의 바이너리 또는 아날로그 센서를 지능형 센서로 탈바꿈할 수 있는 기술이다. 이는 사용자가 단지 데이터를 수집하는 것만이 아니라, 라인 상의 다른 센서들의 상태에 관한 실시간 피드백과 필요한 제조 공정 등을 기반으로 설정을 원격에서 변경할 수 있게 해준다. IO-Link 기술은 프로토콜 스택을 사용하는 공통의 물리적 인터페이스와 설정 가능한 센서 포트를 구현할 수 있도록 하는 IO 디바이스 기술(IO Device Description, IODD) 파일을 통해서 센서들을 서로 교체가 가능하게 해준다. 이는 진정한 플러그-앤-플레이를 지원하며, 실행 중에 파라미터를 재설정하는 것도 가능하게 한다.”
그림 2에서 보듯이, 공장 네트워크 계층에 있어서 IO-Link 프로토콜은 에지 상에 존재하며 주로 센서와 액추에이터로 이루어진다. 많은 경우, 에지 디바이스가 게이트웨이와 통신하는데, 이 게이트웨이는 IO-Link 프로토콜을 선택한 필드버스로 변환한다.
.jpg)
▲그림 2 : IO-Link 프로토콜을 사용하면 지능형 에지 디바이스들을 공장 네트워크에 연결할 수 있다.
IO-Link가 어떻게 차세대 제조 환경이나 산업용 IoT(IIoT)를 가능하게 하는지에 대한 보다 자세한 설명은 아래 기사를 참고할 수 있다. https://www.eletimes.com/io-link-enables-industrial-iot
■ IO-Link 센서 설계
산업용 센서는 견고하고, 크기가 작을 뿐 아니라, 열 발생을 최소화하도록 에너지 효율이 높아야 한다. 대부분의 IO-Link 센서는 다음과 같은 구성 요소들로 이루어진다.
- 센싱 장치와 그와 관련된 아날로그 프런트 엔드(AFE)
- 마이크로컨트롤러(MCU) : 데이터를 처리하고 IO-Link 센서를 위한 경량 프로토콜 스택을 실행한다.
- IO-Link 송수신기 : 물리 계층에 속한다.
- 전원장치와 보호 기능(서지, EFT/버스트, ESD 등으로부터 보호하기 위한 TVS 다이오드)
■ 발열 특성(전력 효율)
IO-Link 센서의 통상적인 구성 요소들을 살펴보았으니 이번에는 센서의 전력 소모에 대해서 가정해 보자. 그림 3에서 모든 수치들은 대략적인 추정값이다. 트랜시버(출력 스테이지) 전력 소모가 센서의 전체적인 시스템 전력 소모에 있어서 가장 중요하다는 것을 알 수 있다.
그림의 왼쪽 그래프부터 차례대로 살펴보면, 맨 왼쪽은 예전 세대 IO-Link 센서의 전력 소모를 보여준다. 오른쪽 그래프로 갈수록, 시간이 흐르면서 MCU와 출력 스테이지(즉, 트랜시버)가 진보함에 따라 총 시스템 전력이 어떻게 낮춰졌는지 알 수 있다.
1세대 IO-Link 트랜시버는 400㎽ 혹은 그 이상을 소모했다. 아나로그디바이스의 최신 세대 저전력 IO-Link 트랜시버는 100㎽ 미만을 소모한다. MCU 또한 전력 소모가 낮아졌다. 예전 MCU는 많게는 180㎽를 소모하는데, 최신 저전력 MCU는 50㎽까지 낮아졌다.
따라서 최신 IO-Link 트랜시버에 저전력 MCU를 결합하면 센서의 총 전력 소모를 400∼500㎽ 대로 낮출 수 있는 것이다.
전력 소모는 발열과 직결된다. 센서의 크기가 작을수록 발열에 대한 요구는 엄격해진다. 8㎜ 직경(M8)의 밀봉 원통형 IO-Link 센서는 최대 전력 소모가 400㎽인데, 12㎜ 직경(M12) 밀봉 원통형 IO-Link 센서는 최대 전력 소모가 600㎽이다.
기술은 계속해서 진보하고 있다. 아나로그디바이스의 최신 IO-Link 트랜시버 제품인 ㎃X14827A는 100㎃ 부하를 구동하면서 단 70㎽밖에 소모하지 않는다. 이는 기술 최적화를 통해 2.3Ω(정격)의 극히 낮은 온-저항(RON)을 달성함으로써 가능해진 것이다.
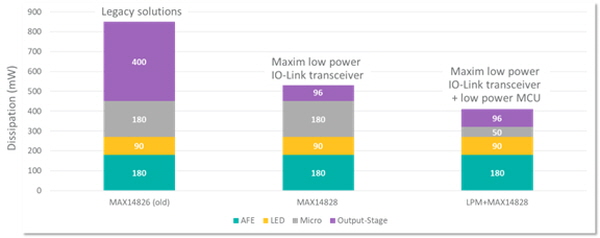
▲그림 3 : IO-Link 산업용 센서의 전력 소모에 대한 가정
3∼5㎃의 극히 낮은 동작 전류를 사용하고 3.3V 또는 5V 전원을 필요로 하는 센서는 LDO를 통해 조절된 전원을 공급할 수 있다. 아나로그디바이스의 IO-Link 트랜시버는 LDO를 내부에 통합하고 있다.
그런데 전류 요구량이 가령 30㎃로 높아지면 이 LDO가 시스템 내의 주된 전력 소모/발열 요인이 될 것이다. 30㎃에서 비교했을 때 LDO의 전력 소모는 600㎽까지 높아질 수 있다.
30㎃일 때 LDO 전력 소모 = (24-3.3) x 30㎃ = 621㎽
이에 비해 DC-DC 벅 컨버터는 30㎃ 센서로 3V 출력 전압을 제공할 때 90㎽만을 소모한다. 이 컨버터의 전력 변환 효율이 90%라고 한다면 (단 9㎃의 전력 손실), 전반적인 전력 소모는 90 + 9 = 99㎽이다.
아나로그디바이스의 최신 IO-Link 트랜시버는 내부에 고효율 DC-DC 레귤레이터를 통합하고 있다(그림 4).
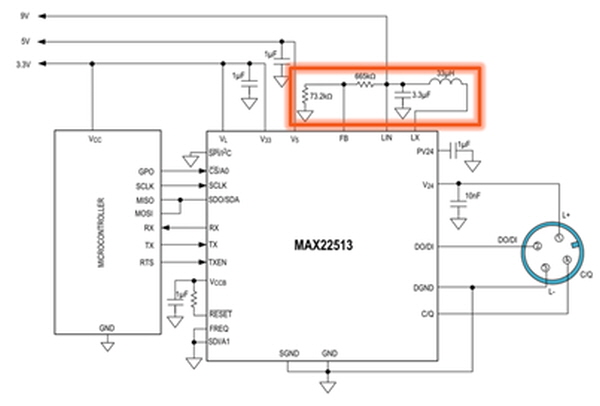
▲그림 4 : 아나로그디바이스의 최신 IO-Link 트랜시버는 집적 고효율 DC-DC 레귤레이터를 포함하고 있다.
■ IO-Link 센서의 크기
모든 산업용 센서에서 크기는 또 다른 중요한 관심사이다. IO-Link 센서에서도 마찬가지다. 크기 축소에 대한 끊임없는 요구로 인해 보드 공간은 갈수록 더 중요해지고 있다.
그림 5는 직경 12㎜ 하우징에서 폭이 10.5㎜인 일반적인 PCB 위에 트랜시버(WLP 패키지)와 DC-DC를 나란히 탑재한 모습을 보여준다. 그러고도 동일 PCB 면에 비아와 와이어들을 위한 공간이 남아 있다. 만약 센서 하우징이 6㎜이면 PCB 폭은 4.5㎜로 줄어든다. 그러면 크기가 작은 WLP 패키지의 칩들을 사용한다 하더라도 PCB의 위아래 양면에 칩을 탑재해야 한다.
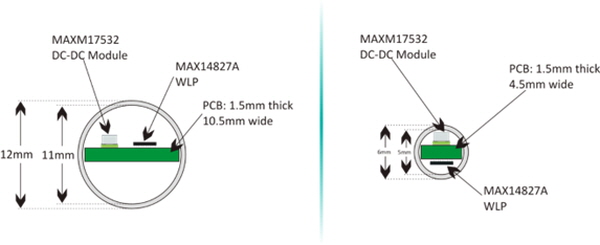
▲그림 5 : 최신 IO-Link 센서 설계에서는 크기 역시 중요한 요소이다.
이처럼 크기를 축소하려면 트랜시버를 WLP(웨이퍼 레벨 패키지)로 제공해야 한다. 아나로그디바이스의 최신 IO-Link 트랜시버는 DC-DC 컨버터를 통합하고 있어 크기 최소화 면에서도 유리하다.
또한 산업용 센서는 열악한 환경에서도 견고하게 동작하도록 설계해야 한다. 다시 말해 TVS 다이오드 같은 보호 회로를 포함해야 한다는 뜻이다(그림 5에서 TVS 다이오드는 표시하지 않았다.) 이와 관련해서 IO-Link 트랜시버의 최대 정격 절대값(Absolute ㎃ximum Ratings) 규격에 주의를 기울일 필요가 있다.
좀 더 자세히 살펴보자. IO의 65V 최대 정격 절대값이 어떻게 센서 서브시스템의 크기를 줄일 수 있게 할까? 통상적으로 이러한 센서는 4개의 핀(GND, C/Q, DI, DO) 사이에서 서지 펄스를 견딜 수 있어야 한다. 아나로그디바이스의 IO-Link 트랜시버는 65V의 최대 정격 절대값을 갖는다. 예를 들어 C/Q와 GND 사이에 1kV/24A 서지라고 해보자.
C/Q와 GND 사이의 전압 = TVS 클램프 전압 + TVS 순방향 전압
최대 정격 절대값이 높으면, 설계 엔지니어는 클램프 전압이 24A일 때 60V이고 TVS 순방향 전압이 24A일 때 1V인 S㎃J33 같은 소형 TVS 다이오드를 사용할 수 있다.
C/Q와 GND 사이의 전압 = 61V
이 값은 아나로그디바이스 트랜시버의 최대 정격 절대값 규격 범위 안에 있다.
그런데 최대 정격 절대값 규격이 이보다 낮으면(업계에서는 45V가 통상적), 전압을 허용 가능한 수준으로 클램프하기 위해서 SMCJ33 같은 훨씬 더 큰 TVS 다이오드가 필요하다. 이 다이오드는 아나로그디바이스 트랜시버가 필요로 하는 것보다 3배 이상 더 큰 것이다.
그러므로 트랜시버 최대 정격 절대값이 낮으면 더 큰 TVS 다이오드가 필요해, 전반적인 센서 설계 크기에 중대한 영향을 미친다. 표 1은 PCB 면적의 차이를 보여준다. 센서가 1kV/24A의 높은 서지를 견뎌야 한다고 가정했을 때이다.
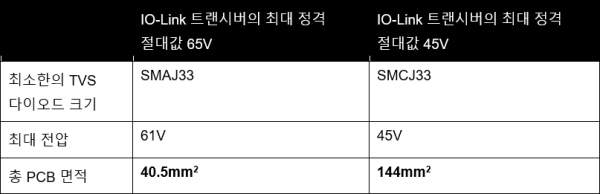
▲표 1 : 65V 최대 정격 절대값이 센서 크기에 있어서 유리하다는 것을 알 수 있다.
차세대 IO-Link 트랜시버는 이보다 더 진보했다. 아나로그디바이스의 최신 IO-Link 트랜시버는 IO-Link 라인 인터페이스 핀(V24, C/Q, DI, GND) 각각에 보호 기능을 포함하고 있다. 모든 핀들이 1.2kV/500Ω 서지 보호뿐 아니라 역 전압 보호, 단락 회로 보호, 핫 플러그 보호 기능을 포함한다.
이들 디바이스는 이 모든 보호 기능을 포함하고 내부에 DC-DC 벅 레귤레이터를 통합하고서도 극히 소형화된 WLP 패키지(4.1㎜ x 2.1㎜)로 제공되므로 소형화된 IO-Link 센서 설계가 가능하게 해준다.
■ 맺음말
그림 6은 아나로그디바이스의 IO-Link 트랜시버 기술이 어떻게 진보하고 있는지 보여준다.
.jpg)
▲그림 6: IO-Link 트랜시버 기술의 진보
1세대 IO-Link 트랜시버 기술은 사용하기 편한 TQFN 패키지에 LDO를 통합함으로써 소형 센서 설계의 요구 사항을 충족했다. 전력과 크기 이슈가 점점 더 중요해짐에 따라 2세대 트랜시버 기술은 낮은 RON을 제공하여 추가적으로 전력 소모를 감소시키고, 크기도 더 작아진 WLP 패키지가 가능하도록 하는 기술을 적용함으로써 전력 소모를 최적화했다.
최신 세대의 트랜시버는 보호 기능을 포함하고 고효율 DC-DC 벅 레귤레이터를 통합함으로써 센서 서브시스템의 크기를 보다 더 줄이고 발열 특성도 개선하였다.
갈수록 더 많은 산업용 센서에 IO-Link 기술이 사용됨에 따라 이러한 디바이스 규격은 작고, 견고하며, 전력 효율적인 센서를 달성하는 데 있어서 매우 중요해졌다.
※ 기고자
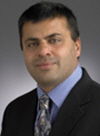
수헬 다나니(Suhel Dhanani) 아나로그디바이스 산업 및 헬스케어 사업부 비즈니스 개발 디렉터