기존의 공장을 자동화하는 개념을 넘어 공장 설계부터 무인자동화까지 연결성과 디지털 트윈을 통한 공정개발로 데이터를 통한 적극적 운영관리를 수행할 수 있는 스마트제조 데모공장이 국내에서 운영을 시작해 향후 스마트팩토리 구축의 모델 및 공정기술 개발에 기여할 것으로 기대를 모으고 있다.
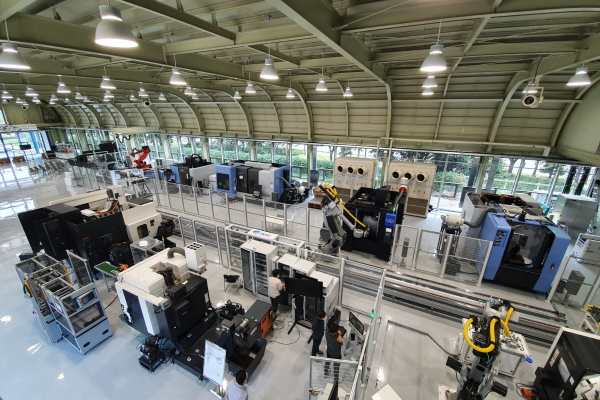
▲‘스마트제조 데모공장’ 내부
초연결성 기반 유연생산 체계 갖춘 진정한 스마트팩토리 비전 제시
디지털 트윈 플랫폼, 엣지-클라우드 활용 데이터 기반 AI 운영관리
지난 7월28일 기존의 공장을 자동화하는 개념을 넘어 제품 기획·설계부터 공정 설계·개발 및 생산 적용까지 디지털 트윈을 통해 최적화된 인공지능 운영을 수행하는 고도화 스마트팩토리가 공개됐다. 특히, 중소중견 기업이 의뢰한 초정밀 가공/조립/검사등 주요 공정을 개발 지원하고, 이를 시생산으로 검증해 실생산까지 원-스탑 지원하는 국내 유일의 ‘스마트제조 공정혁신센터’가 처음으로 국내에 개소한 것이다.
본지는 최근 한국전자기술연구원(KETI)이 경남 창원시에 개소한 ‘스마트제조 공정혁신센터’를 방문했다.
‘스마트제조 공정혁신센터’는 국가 스마트그린산단 1호 사업으로, 기계가공분야의 국내 최고 산업단지인 창원국가산에 위치하고 있다. 디지털 트윈, 산업IoT 플랫폼, 5G, 인공지능 등 첨단 ICT와 제조기술의 융합을 통해 미래 제조기술의 방향을 제시함과 동시에 구축된 약 6,800㎡의 공장 인프라를 활용한 제조기업이 위탁한 공정개발, 실생산의 구체적인 미션을 수행한다.
독일에서는 디지털 트윈 기반으로 유연생산체계를 갖춘 공장이 4차 산업혁명의 스마트팩토리라고 표현을 하는데 이렇게 되기 위해서는 공장 내 모든 생산요소가 연결되어 데이터화 할 수 있어야 한다.
이와 함께 공장안에서 제품을 생산하고 운영하는 모든 것을 디지털 트윈으로 구현하고, 그 위에 각종 제조 서비스를 클라우드 등으로 확장 가능할 수 있는 단계로의 진화가 필요하다.
‘스마트제조 공졍혁신센터’를 방문하면 우선 현대위아, 두산공작기계, 화천, 지멘스, 화낙과 같은 다양한 공작기계와 산업용 장비들이 눈에 띈다.
우선 이 장비들은 초고속 초저지연 통신을 지원하는 5G와 TSN(Time Sensitive Network) 기술을 활용한 유무선 네트워크들로 연결돼 있으며, OPC-UA(Open Platform Communications Unified Architecture)라는 국제표준 산업 IoT 기술을 이용해 연결돼 있다. 초연결의 제품개발부터 생산까지 하이퍼 커넥션 되어 있는 상황이다.
자동화 레벨과 공장 운영을 통합 관리하는 제조응용 레벨간 IT/OT 융합을 자유롭게 만들 수 있는 하이브리드 구축형 클라우드도 구축돼 있다.
전공정의 세부적인 부분까지 모두 데이터화 디지털화가 가능하고, 이를 통해 전공정을 예측하고 인공지능으로 운영할 수 있는 것이 가능해 졌다.
‘스마트제조 공정혁신센터’를 총괄하는 한국전자기술연구원 송병훈 센터장은 이러한 첨단 기술을 활용한 초연결 및 최적화된 AI 공장 운영의 핵심은 ‘디지털 트윈 플랫폼’에 있다고 밝혔다.
디지털 트윈은 현실 속의 장비, 각종 사물 등을 컴퓨터 속 가상환경 동일하게 구현해 가상의 제조 환경에서 발생할 수 있는 다양한 상황을 사전에 컴퓨터 시뮬레이션 함으로써 결과를 미리 예측하는 기술이다.
최근 센터는 실제 항공기, 방산, 정밀기계 분야들의 기업들과 협의해서 제품에 대해 파일럿 생산도 진행을 계획 중이다.
즉 센터는 디지털 트윈 데이터를 기반으로 공정 설계, 생산계획 수립, 생산운영 관리, 품질 관리에 이르는 제조 전영역의 운영까지 할 수 있으며 모든 과정은 자체 구축된 하이브리드 클라우드 플랫폼을 통해 관제 된다.
센터는 데이터 기반으로 △공작기계의 선제적 관리 △공구/공작물 세팅과 같은 예방적 관리 △열변위 관리 방안 등 적극적 제어 △정보 관리/보정 등을 관리하고, 인공지능(AI) 기술을 통해 자율 운영하는 모습을 보여 주고 있으며, 노하우를 프로그램에 선정된 기업들을 교육하고 있다.
국내외 다양한 공급기업과 수요기업이 센터의 1:1 매칭 프로그램을 통해 만남을 가지고 있다.
송병훈 센터장은 “우리는 신제품 개발부터 운영, 서비스까지 제조 전 영역에 5G 기반으로 초연결이 가능한 디지털 규격을 만들고 있다. 또한 여러 제조 데이터를 통해 인공지능(AI) 관리를 할 수 있는 핵심 기술을 연구하고 있다. 제조 디지털 트윈 플랫폼을 통해 센터를 운영하며, 수요 기업들에 적용 가능한 구체적인 사례들을 제시할 것”이라고 밝혔다.
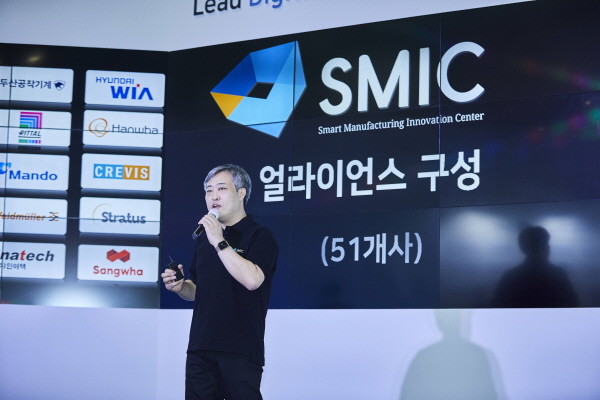
▲송병훈 KETI 스마트제조 공정혁신센터장
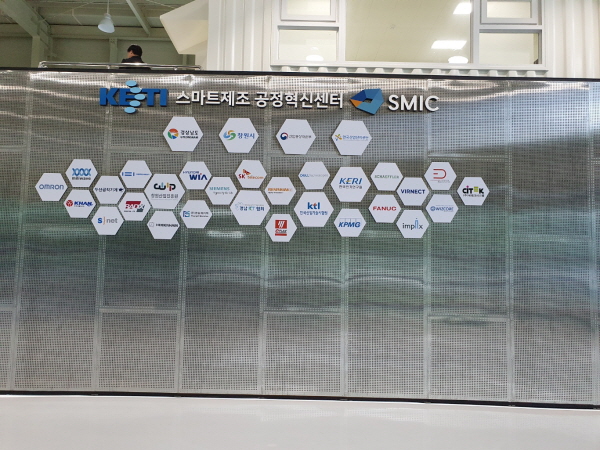
▲‘스마트제조 데모공장’에 참여한 기관 및 기업들의 이름이 적힌 컨테이너에는 이 공장의 모든 데이터가 수집되는 데이터센터가 구축돼 있다.
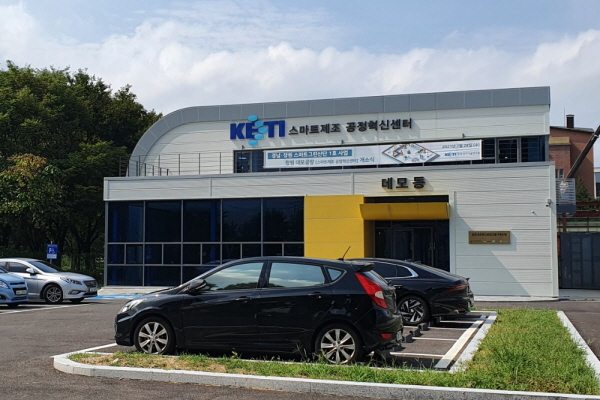
▲‘스마트제조 데모공장’ 외부 전경