선형 모터(linear motor)에 대해 마우저 일렉트로닉스(Mouser Electronics)의 Bill Schwebe(빌 슈위버)에게 들어봤다.
“선형 모터 다양한 산업·특수 응용 분야서 매력적 선택”
모션 시스템 대역폭·강성 높아지고, 더 나은 반복성·정확도 지원
높은 비용·복잡성 불구 높은 정밀도·응답성 요구 분야에 이상적
대부분의 사람들은 전기 모터를 생각할 때, 회전 운동을 제공하고 샤프트(Shaft, 축)를 돌리는 모터를 떠올린다. 이는 많은 사람들이 익숙하게 접하는 모터이기 때문이다.
하지만. 또 다른 종류의 전기 모터가 있다. 그것은 선형 모터(linear motor)다(그림 1).
이 모터는 비교적 덜 알려져 있지만, 직선 운동이 필요한 다양한 분야에서 널리 사용된다. 응용 사례로는 대형 천장 크레인 및 빌딩 엘리베이터, 중형 무벨트 컨베이어 그리고 창문 커튼, 반도체 제조 공장에서의 웨이퍼를 처리하는 소형 장비와 카메라 렌즈의 초점을 조절하는 미세 모터까지 포함된다. 말할 필요 없이, 이 외에도 매우 다양한 용도로 활용된다.
▲그림 1: 선형 모터는 회전 운동을 제공하는 일반적인 전기 모터와 달리, 고정자(stator)를 ‘펼친(unwrapping)’ 형태로 설계하여, 직선 운동을 직접 생성하는 전기 모터다.
선형 모터의 중요한 특징 중 하나는, 기존의 회전 모터에 기어, 리드 스크류(lead screw), 볼 스크류(ball screw), 또는 벨트와 같은 기계적 장치를 추가하여 선형 운동으로 변환한 장치가 아니라는 점이다. 이러한 변환 장치는 선형 액추에이터(linear actuator)라고 하며, 전자기계 시스템 설계에서 중요한 역할을 한다.
반면, 선형 모터는 본질적으로 선형 운동을 직접 출력하는 모터로써, 선형 운동으로 ‘변환(converted)’되기 위한 회전 운동이 없다. 선형 모터는 직선(선형) 운동을 제공하는 방법 중 하나이며, 이 외에도 공압(압축 공기), 유압(압력이 가해진 유체), 전기 동력을 활용하는 방식이 있다(그림 2).
이러한 초기 선형 모터들은 낮은 가속도의 장치로 시작되었지만, 최근의 무브러시 직류(BLDC, Brushless Direct Current) 모터 기술과 고성능 드라이브 전자 장치의 발전으로 인해 이러한 한계를 대부분 극복하였다.
▲그림 2: 선형 액추에이터 제품군에는 공압, 유압 및 전기 방식들을 포함하며, 각각 하위 유형들이 존재한다.
■ 고정자가 펼쳐진 상태로 움질이는 선형모터
전통적인 전기 모터에서는 로터가 움직이지 않는 고정자 내부에서 회전한다. 반면, 선형 모터에서는 고정자가 ‘펼쳐진(unwrapped)’ 상태로 평평하게 놓여 있고, 로터가 직선으로 그 위를 지나간다. 회전 모터에서와 마찬가지로 움직이는 로터 표면은 고정자 표면에 닿지 않지만, 이를 정렬하기 위한 가이드 레일이나 트랙이 있을 수 있다. 고정자는 알루미늄이나 구리로 만든 평평한 코일의 트랙이 되고, 로터는 움직이는 플랫폼이 된다.
선형 모터는 교류(AC) 전원과 서보 컨트롤러로 구동되며, 이는 종종 회전 모터와 동일한 유형이 사용된다. 코일의 전류 위상은 각 코일의 극성을 변경하도록 제어되고 조정된다.
로터 내 전류가 흐르는 전자기 코일과 고정자 내 영구 자석 사이를 교대로 작용하는 흡인력과 반발력이 선형 힘을 생성하여 로터가 고정자를 따라 움직이도록 한다.
회전(로터리) 모터와 마찬가지로, 전류 변화율이 이동 속도를 제어하며, 전류의 크기(암페어 수)가 생성되는 힘을 결정한다. 결과적으로, 전자석에 대한 전력 공급의 타이밍(위상)을 관리함으로써 정밀한 움직임을 제어할 수 있다.
■ 여러 매개변수로 선형 모터 성능 결정
선형 모터의 성능을 결정하는 데에는 여러 가지 매개변수가 있다. 그중 주요한 매개변수는 다음과 같다.
- 지속 추력(Continuous thrust force): 과열없이 모터 권선에 공급할 수 있는 최대 정격 전류
- 최대 추력(Peak force): 선형 모터의 최대 출력 힘
- 전체 고정자 길이(Overall stator length): 고정 자석 트랙의 길이
- 슬라이더 또는 캐리지 이동거리(Slider or carriage travel): 움직이는 코일의 실제 이동범위
- 최대 속도(Maximum speed): 선형 모터의 최고 속도
- 최대 가속도(Maximum acceleration): 선형 모터의 최고 가속도
■ 반복성·정확도 지원
선형 모터의 주요 장점 중 하나는 기어박스, 커플링과 같은 변속 부품의 가변적인 손실이 발생하지 않으며, 이러한 부품과 관련된 백래시(backlash, 유격) 및 모션(운동)/공진 오류 문제가 없다는 점이다. 따라서 모션(운동) 시스템의 대역폭(bandwidth)과 강성(stiffness)이 훨씬 높아질 수 있으며, 그 결과 더 나은 반복성과 정확도를 지원할 수 있다.
앞서 언급했듯이, 선형 모터만이 잘 제어되는 선형 운동(모션)을 제공하는 유일한 방법은 아니다. 많은 경우, 회전 모터와 볼 스크류(ball screw) 또는 선형 액추에이터로써의 여러 메커니즘을 갖춘 저렴한 솔루션을 사용하여 동일한 모션 효과(성능은 동일하지 않더라도)는 달성할 수 있다.
그렇다면 왜 설계 엔지니어가 볼 스크류(ball screw)나 선형 액추에이터 대신, 선형 모터를 사용해야 할까. 간단히 말해, 선형 모터는 더 빠른 동작, 가속도, 그리고 매우 높은 정확도를 제공하는 데 유리한 반면, 볼 스크류와 선형 액추에이터는 더 높은 추력(force)과 낮은 비용을 제공한다는 것이다.
선형 액추에이터에 비해 선형 모터의 상대적 특성을 자세히 살펴보면 다음과 같다.
- 더 높은 속도 및 해상도(Higher speed with resolution): 고성능 선형 모터는 초속 3미터(3m/sec)의 속도와 1마이크론(1㎛) 해상도를 달성할 수 있으며, 초속 5미터(5m/sec; 약 200 inch/sec) 이상의 속도도 가능하지만, 이 경우에는 해상도가 다소 낮아질 수 있다.
- 고정밀(High precision): 정확도(accuracy), 해상도(resolution), 반복성(repeatability)은 주로 피드백 장치의 성능, 제어 시스템의 대역폭, 그리고 비용에 의해 결정된다.
- 빠른 응답(Fast Response): 선형 모터의 고유 응답 속도는 기계적 변속 장치보다 1∼2배 빠른 속도로 응답할 수 있으며, 결과적으로 더 빠른 가속 및 짧은 정착(settling) 시간을 제공한다.
- 강성(Stiffness): 선형 모터의 강성은 루프 이득(loop gain)과 전류 구동(current drive)에 의해 결정되며, 기계식 연결(링크) 방식보다 높다.
- 백래시(유격) 없음(Zero backlash): 기계적 변속 부품이 없기 때문에 백래시(유격) 또는 헐거운 움직임(느슨함)이 발생하지 않는다.
- 마모 없음(Zero wear): 평평한 고정자(stator) 트랙과 움직이는 로터(rotor) 사이의 직접적인 접촉이 없기 때문에 마모나 마찰이 없다. 다만, 가이드 트랙(guide track)은 마모될 수 있지만, 적절한 설계와 크기 조정을 통해 관리할 수 있다.
엔지니어링은 우선순위와 절충점(트레이드오프, trade-off)을 균형 있게 맞추는 과정이며, 선형 모터에도 상대적인 단점은 존재한다.
- 비용(Cost): 선형 모터는 이동 레일의 전체 길이에 걸쳐 희토류 자석이 필요하기 때문에 부분적으로 더 비싸다. 반면, 회전 모터의 경우는 자석이 로터(rotor) 주변에만 필요하다. 마찬가지로, 선형 피드백 시스템은 이동 경로의 길이로 인해 회전 모터의 피드백 시스템보다 더 많은 비용이 든다.
- 전원 케이블 조정(Coordinated power cables): 모터의 이동하는 부위에 연결된 전원 케이블은 모터와 함께 구부러지고 이동해야 하므로 설계 문제가 발생할 수 있다.
- 보호(Protection): 선형 모터는 상대적으로 외부에 노출되어 있으므로, 작동 환경으로부터 이를 보호하고 둘러싸는(Enclose, 인클로징) 것이 어려울 수 있다.
- 대역폭(Bandwidth): 선형 모터는 모터와 부하(load) 사이에 기계적 감속 장치가 없으므로, 더 높은 대역폭을 갖는 드라이브와 루프 제어가 필요하다. 또한, 서보 응답 대역폭도 더 빨라야 한다.
- 힘 대비 크기 비율(Force versus size): 선형 모터는 회전 모터 정도의 콤팩트한 ‘힘 생성기(force generator)’가 아니다. 회전 모터의 경우 변속 장치를 통해 기계적 이점을 얻을 수 있지만, 선형 모터는 출력 대비 부피가 낮다.
- 자체 발열(Self-heating): 대부분의 선형 모터 응용에서 모터는 부하에 직접 부착되므로, 전력 손실(I²R) 또한 부하로 전달된다. 특히 코일을 제자리에 고정하는 데 사용되는 에폭시(epoxy)는 열을 효과적으로 방출하지 않기 때문에, 일부의 경우에는 추가적인 열 관리가 필요하다.
■ 선형 모터의 비전통적 응용 분야
선형 모터는 두 가지 다소 비전통적인 응용 분야에서도 사용된다. 바로 자기 부상(magnetic levitation, maglev) 철도와 레일건(rail gun)이다. 자기부상 철도는 수년 동안 추진되어 왔지만, 일부 지역에서만 건설되어 사용되었다.
이 열차는 선형 모터의 고정자를 트랙으로, 열차 본체를 로터로 사용하여 시속 300km에서 400km(대략 200mph에서 260mph)의 속도에 도달할 수 있다. 열차는 트랙 위에 떠 있으며(즉, 부상), 마찰이 없는 배열로서 둘 간의 접촉이 없다는 것이 상당한 이점이다(그림 3).
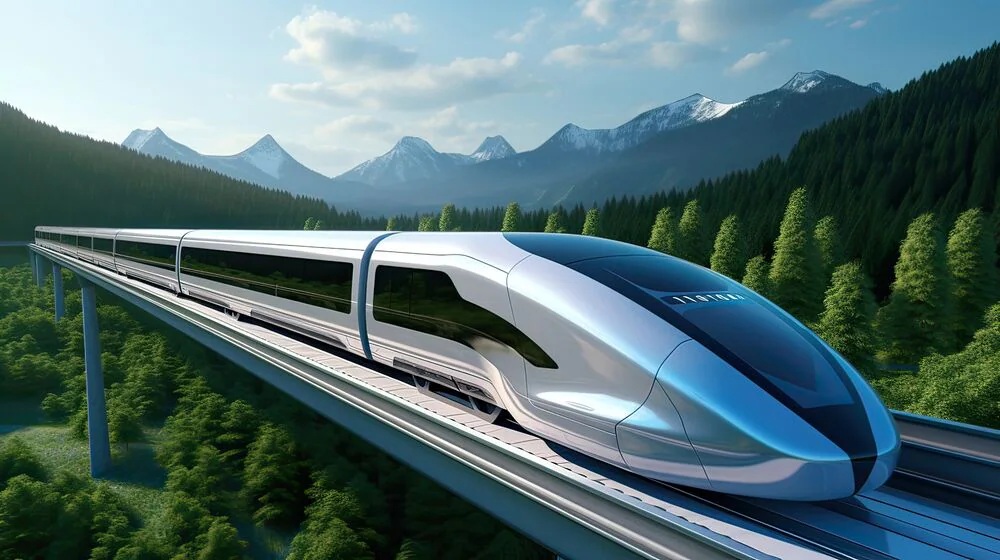
▲그림 3: 자기 부상 열차(Maglev railway)는 드물지만, 최대 순항 속도가 300km/h에 달하며, 최고 속도는 431km/h에 도달한 기록이 있다. 즉, 30km 이동하는 데 약 8분이 소요된다.
한편 군사용 레일건(rail gun)은 전투함에서 시험되고 검증된 개념이지만, 당분간 보류된 상태다. 이 시스템은 약 10미터 길이의 선형 모터를 사용하여 무게가 약 1kg인 소형 비폭발성 탄환(수동 발사체)을 초속 2,500미터(약 5,600mph)까지 가속한다. 탄환(발사체)은 폭발 없이 충돌시의 운동 에너지만으로 목표물을 파괴한다.
그러나 자기 부상 열차와 레일건의 실용화에는 여러 가지 주요 장애물이 있다. 자기 부상 열차의 초기 건설 비용은 기존 열차보다 훨씬 높으며, 지속적인 운영 비용(특히 전력)과 유지보수 비용도 높다. 또한, 레일건 기술은 향후 지상 배치용으로 다시 연구될 가능성은 있지만, 크기, 설치, 마모 및 전력 수요와 관련하여 해결해야 할 과제와 물류 관련 문제는 여전히 존재한다.
■ 높은 비용·복잡성 불구 성능상의 이점이 더 커
선형 모터는 고속, 빠른 가속, 정밀한 선형 위치 제어가 필요한 응용 분야에서 독특한 장점을 제공한다. 설계 및 구현에 있어 높은 비용과 복잡성과 같은 도전 과제가 있을 수 있음에도 불구하고, 이러한 단점보다 성능상의 이점이 더 클 때가 많다. 선형 모터는 백래시(backlash, 유격) 및 기계적 변속 부품과 관련된 가변적인 손실 문제를 제거하며, 높은 정밀도와 응답성이 요구되는 응용 분야에 이상적이다.
그러나 설계 엔지니어는 선형 모터와 회전 모터 기반 선형 액추에이터 등과 같은 대체 솔루션을 신중하게 비교하고, 특정 애플리케이션의 요구 사항을 평가해야 한다. 기술의 지속적인 발전으로 선형 모터는 다양한 산업 및 특수 응용 분야에서 여전히 매력적인 선택이다.
# 글쓴이
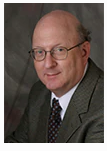
Bill Schweber(빌 슈위버)는 Mouser Electronics의 기고 작가이자 전자 엔지니어로, 전자 통신 시스템에 관한 세 권의 교과서를 집필했으며, 수백 편의 기술 기사, 의견 칼럼, 제품 관련 기사를 작성했다. 과거에는 EE Times에서 여러 주제별 기술 웹사이트를 관리하는 웹사이트 관리자였으며, EDN에서 수석 편집자(Executive Editor) 및 아날로그 편집자(Analog Editor)로도 활동했다. Analog Devices, Inc.(아날로그 및 혼합 신호 IC의 주요 공급업체)에서 마케팅 홍보 업무를 담당했으며, 이 역할을 통해 기술 PR 기능 측면에서도 활동했다. 즉, 회사 제품, 스토리, 메시지를 미디어에 전달하는 역할을 수행하는 동시에, 미디어 측에서 이를 수용하는 역할도 경험했다. Analog에서 MarCom 역할을 맡기 전에는 존경받는 기술 저널의 부편집장을 역임했으며, 제품 마케팅 및 애플리케이션 엔지니어링 그룹에서도 근무했다. 그 전에는 Instron Corp.에서 아날로그 및 전력 회로 설계와 재료 테스트 기계 제어를 위한 시스템 통합 업무를 직접 수행했다. 그는 매사추세츠 대학교(University of Massachusetts)에서 전기공학 석사(MSEE), 컬럼비아 대학교(Columbia University)에서 전기공학 학사(BSEE) 학위를 취득했으며, 등록된 전문 엔지니어(Registered Professional Engineer) 자격을 보유하고 있다. 또한 고급 아마추어 무선(Advanced Class amateur radio license) 면허를 가지고 있다. Bill은 MOSFET 기본 개념, ADC 선택, LED 구동 등 다양한 엔지니어링 주제에 대한 온라인 강좌를 기획, 집필, 강의한 경험도 있다.