자동화 애플리케이션은 더 많은 산업용 로봇과 자동화 기계를 통합하고 있다. 산업용 로봇은 매번 동일한 정밀도로 다른 작업을 수행할 수 있지만, 정밀한 모터 구동 제어 없이는 불가능하다. TI의 C2000 제품군은 모터 제어 시스템 설계자가 고해상도 전류 및 전압 감지 피드백을 설계하는 데 도움을 준다. C2000 제품군의 F28004x 제품 및 37x 제품군은 주변장치 IP가 동일 세대이므로 코드 호환율이 뛰어나다. 그리고 고성능의 ADC를 내장하고 있으며, 외부에 별도의 로직 IC가 필요 없는 단일 SoC로, MCU+FPGA 아키텍처보다 시스템 비용을 절감할 수 있다.
고해상도 전류 및 전압 감지 피드백 설계
모터 제어 시스템 설계 시 최대 과제로 꼽혀
고성능 ADC 내장 TI C2000, 시스템 비용 절감
자동화 애플리케이션은 더 많은 산업용 로봇과 자동화 기계를 통합하고 있다.
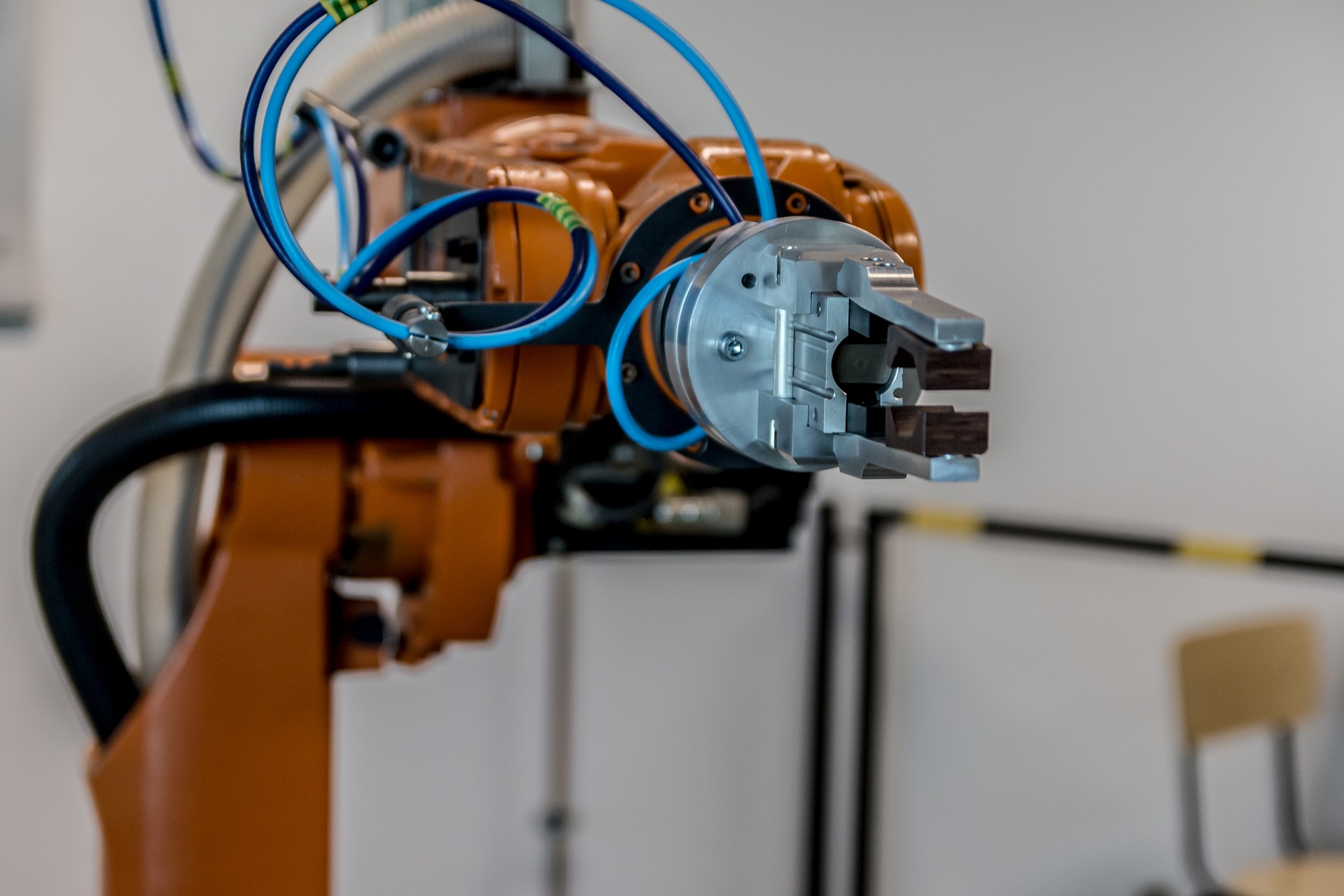
로봇의 정밀한 작업은 정밀한 모터 구동 제어로만 가능하다
로봇은 엔진 블록을 집어 차량 새시에 정확히 놓고, 원래 위치로 돌아와 매번 동일한 정밀도로 다른 작업을 수행할 수 있다. 그러나 이러한 작업들은 정밀한 모터 구동 제어 없이는 불가능하다.
고해상도 전류 및 전압 감지 피드백을 설계하는 것은 모터 제어 시스템에서 가장 큰 과제다. 잠재적인 아날로그 신호 손실, 또는 간섭을 피하기 위해 대부분의 경우 피드백 신호의 디지털화를 센서에 가능한 가깝게 증가시키고자 할 것이다.
이 경우, 디지털 피드백 신호는 타이밍에 잠재적인 문제를 일으킬 수 있다. 클럭 속도가 증가하고 샘플링 속도가 높아지면서 타이밍 윈도가 좁아지기 때문이다. 클럭 및 데이터 신호 간 다른 추적 길이 문제를 악화시키기도 한다.
10월 30일, e4ds.com에서 열린 웨비나에서는 이러한 설계 과제의 해결책이 될 수 있는 TI의 C2000 제품군을 포함하여 공장 자동화 애플리케이션에 대한 전반적인 설명을 제공했다. 기사의 상세 내용은 해당 웨비나에서 확인 가능하다.
고해상도 전류 및 전압 감지 피드백 설계 과제의 해결책
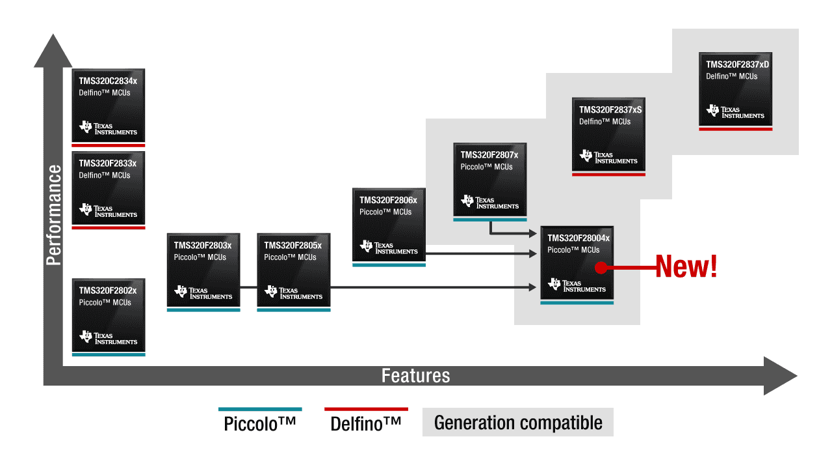
C2000 제품군
C2000 제품군은 성능 및 주변장치들의 특징에 따라 위와 같이 구분할 수 있다.
TI가 가장 최근에 출시한 F28004x 제품 및 37x 제품군은 주변장치 IP가 동일 세대이므로 코드 호환율이 뛰어나다.
TI C2000 MCU는 현재 로우 및 미들 엔드 제품을 위한 피콜로(Piccolo)와 하이 엔드 제품을 위한 델피노(Delfino)라는 두 제품군으로 출시됐다.
공장 자동화와 서보 제어기에 최적인 37x 제품군은 연산 가속을 위해 코어를 개선했으며 아날로그 IP를 대거 채용했다. F28004x 제품은 37x 제품군의 IP을 대부분 채용하면서도 가격을 낮춤으로써 가전제품 및 EV(Electric Vehicle), 혹은 하이브리드 EV의 파워트레인 애플리케이션에도 쓰일 수 있다.
37x 제품군은 듀얼 코어 CPU 및 듀얼 CLA를 통해 최대 800MIPS의 연산 성능을 발휘한다. 37x 제품군부터 삼각함수 및 나눗셈을 1에서 2사이클에 수행할 수 있는 TMU 모듈이 처음으로 적용되어 모터 제어의 FOC 연산 능력을 극대화했다.
또한, 독립적인 ADC 컨버터를 최대 4개까지 가지고 있어 최대 초당 14M의 고속 샘플링이 가능하며, 과전류/과전압의 트립 기능을 위한 윈도 비교기를 최대 8채널 가지고 있다.
F28004x 제품은 37x 제품군에는 적용되지 않은 프로그래머블 OP-AMP를 최대 7채널 내장했다. 따라서 모터 제어 시 상전류 측정을 위해 션트(Shunt)를 사용할 경우, 외부에 별도의 신호증폭용 OP-AMP를 사용하지 않고도 션트의 출력 신호를 직접 MCU로 연결할 수 있다.
또한, 독립적인 ADC도 3개의 모듈을 가지고 있어 3상 모터 제어 시 3상의 전류를 동일 시점에서 센싱이 가능하게 되어 제어 성능 향상에 기여한다.
F28004x 제품은 내부 PLL을 이용해 최대 100Hz로 동작할 수 있으며, CLA를 포함해 최대 200MIPS의 연산 능력을 가지고 있다. 기존 피콜로 제품군은 대부분 고정소수점 코어로 되어 있었지만, F28004x는 부동소수점을 하드웨어적으로 처리할 수 있는 FPU를 가지고 있다. 이로 인해 사용자들은 부동소수점 형태의 C-코드를 손쉽게 개발할 수 있다.
32비트 FPGA와 ASIC의 단점을 극복한 C2000 MCU
많은 산업용 인버터 및 서보 드라이브 제조사들은 상용 32비트 MCU들이 제공되지 않는 기능들을 구현하기 위해 FPGA나 ASIC을 별도로 추가한다.
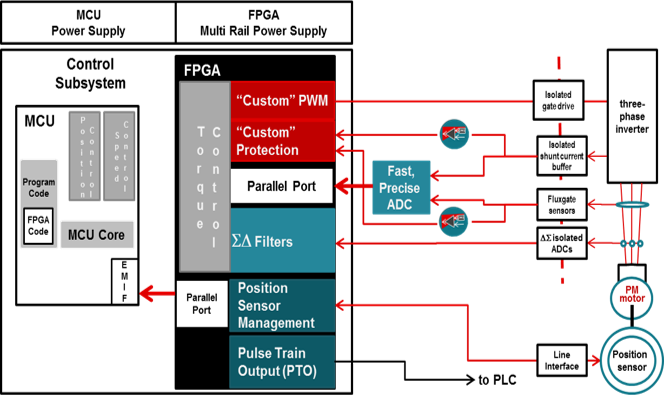
FPGA나 ASIC에 인코더와 필터 모듈을 구현하는 것은 비용도 많이 들고 복잡하다
그러나 위치센서용 인코더나 시그마-델타 필터 모듈을 FPGA나 ASIC에 구현하는 것은 시스템 비용과 개발의 복잡도를 증가시킨다. FPGA 단품의 가격 상승도 있지만, FPGA을 사용함으로써 별도 전원 IC 및 외부 ADC 컨버터 추가로 인한 가격 상승도 있다. 또한 FPGA의 VHDL 코드 개발을 위해 전문 인력을 추가 확보해야 되는 문제점도 있다.
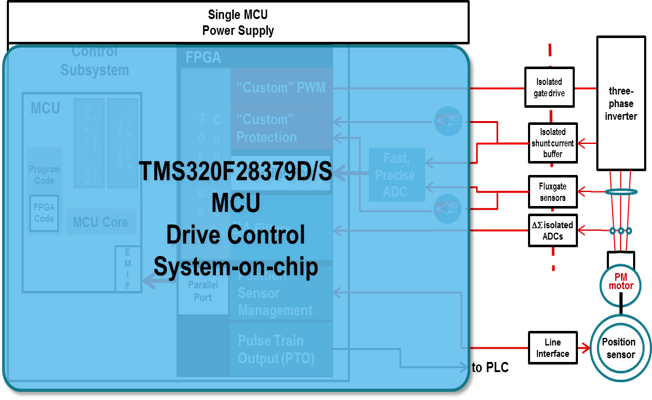
단일 SoC를 사용하면 MCU+FPGA 아키텍처보다 많은 자원을 절약할 수 있다
만일 고성능의 ADC를 내장하고 있으며, 외부에 별도의 로직 IC가 필요 없는 단일 SoC를 사용한다면 MCU+FPGA 아키텍처보다 시스템 비용을 절감할 수 있다.
TI의 DesignDRIVE 기술을 탑재할 수 있는 C2000 MCU는 상용 MCU로써 높은 단계의 시스템 통합을 구현해내며, 개발 기간 및 비용을 단축할 수 있는 장점을 가지고 있다. TI의 DesignDRIVE 기술을 경험할 수 있는 자료들은 TI의 웹사이트에 공유되어 있다.
C2000 MCU와 EtherCAT을 함께 사용하는 방법
공장 자동화에 가장 많이 적용되는 통신방식 중 하나인 EtherCAT을 C2000 MCU와 함께 사용하기 위해서는 크게 두 가지 방법이 있다.
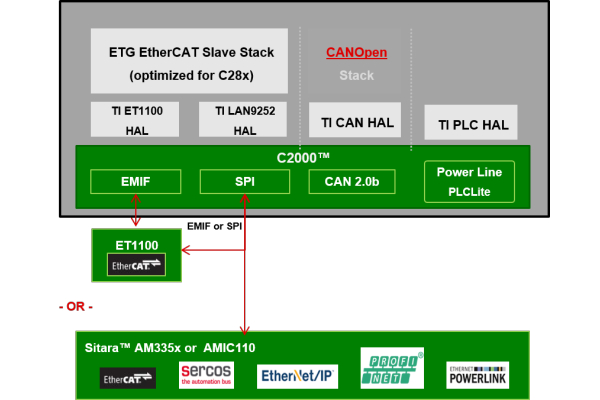
EtherCAT을 C2000 MCU와 함께 사용하는 두 가지 방법
첫 번째 방법은 백오프(Backoff) 사의 ET1100을 EMIF나 SPI로 C2000과 연결하는 것이다. ET1100의 레지스터 액세스를 위한 드라이버 파일은 TI가 제공하고 있으며, C28x에 최적화된 EtherCAT 슬레이브 스택은 ETG(EtherCAT Technology Group)에서 받을 수 있다. TIDM-DELFINO-ETHERCAT이라는 TI 레퍼런스 디자인을 활용하면 좀 더 쉽게 C2000 MCU에서 EtherCAT을 설계할 수 있다.
두 번째 방법은 ET1100과 호환될 수 있는 TI의 AMIC110 통신 프로세서를 사용해 EtherCAT의 슬레이브와 마스터를 구현하는 것이다. AMIC110은 ARM Cortex A8 core을 사용하고 있으며, EtherCAT뿐만 아니라, 거의 모든 산업용 통신 프로토콜을 지원한다. C2000 MCU와는 SPI 통신으로 연결될 수 있으며, EtherCAT을 위한 레지스터 MAP은 백오프(Backoff) 사의 ET1100과 호환성을 유지한다.
최근 공장 자동화에 많이 적용되는 또 다른 통신방식인 CAN을 활용하는 CANOpen 프로토콜은 TI의 서드 파티인 시마(Simma) 소프트웨어를 통해 해당 스택을 유료로 공급받을 수 있다.